During World War II, the U.S. military faced a unique problem: ensuring the quality of bullets without testing every single one. The solution was a sampling method known as MIL-STD-105, which laid the foundation for the Acceptable Quality Limit (AQL). This methodology allowed inspectors to assess a subset of bullets and determine whether an entire batch met quality standards—balancing efficiency with reliability.
Fast forward to today, AQL remains an essential tool in quality control, particularly in product inspections for brands manufacturing overseas. It helps answer two critical questions:
- How many products should be inspected to ensure a shipment’s overall quality?
- What is the maximum number of defects that can be tolerated before the shipment is rejected?
For ecommerce businesses relying on third-party manufacturers, AQL ensures consistency, mitigates risk, and safeguards brand reputation. Let’s dive into what does AQL mean, and how it applies to quality inspections.
What Is Acceptable Quality Limit (AQL)?
AQL is a statistical method used to determine the maximum allowable number of defective goods while still considering the overall shipment acceptable. In ISO 2859-1, AQL is defined as the "worst tolerable quality level." It is a pertinent tool in quality control, helping manufacturers manage product quality through structured sampling and inspection techniques.
Rather than inspecting an entire shipment, AQL uses a representative sample to determine whether the overall batch meets predefined quality standards or requires rejection.
Since quality expectations vary, AQL is not a fixed standard. It varies based on industry norms, product risk levels, and agreements between buyers and suppliers. For instance:
- Medical devices typically have a lower AQL threshold due to high safety risks.
- Consumer electronics may allow for minor cosmetic defects but enforce strict performance requirements.
- Fashion and apparel may have a slightly higher AQL for minor defects like loose threads but a near-zero tolerance for stitching failures.
Defect Classification and AQL Levels
In quality control, defects are categorized into three levels: Critical, Major, and Minor. Each category has a corresponding AQL threshold, which helps determine the acceptable number of defects before a shipment is rejected.
Once an AQL standard is agreed upon, it is used as a benchmark during pre-shipment inspections to ensure product quality meets buyer expectations. By defining these thresholds, importers can balance quality control with production feasibility, reducing waste and ensuring customer satisfaction.
Read More: 5 Factory Inspection Mistakes & Best Practices for Quality Control
What Does AQL 2.5 Mean?
AQL 2.5 is a specific application of the ISO 2859-1 standard, representing an acceptable defect rate of 2.5% in a given sample size. This means that for every 100 units inspected, a maximum of 2.5 defective units is allowed for the shipment to be considered acceptable. Under AQL 2.5, goods are accepted with a defect rate of 2.5%, regardless of the nature of the defect. However, the impact of different defects varies across products and industries. For example:
- A 0.5% critical defect rate in medical devices could be far more damaging than 2.5% minor defects in apparel.
- A defect in a structural component of a vehicle is significantly more severe than a slight color variation in home decor.
AQL 2.5 is beneficial for balancing inspection efficiency and cost-effectiveness, ensuring that the total quantity of products do not require 100% inspection, which would be time-consuming and costly. Instead, it determines the appropriate sample size and rejection criteria based on statistical models. A tighter AQL may be needed for high-risk products, whereas lower-risk items can afford a more lenient standard. This flexibility makes AQL 2.5 an essential tool to ensure consistent product quality.
How Does AQL Work?
AQL inspections provide a risk-based, efficient method to control product quality, ensuring that brands can balance cost, time, and quality. These inspections rely on a predefined AQL sampling plan, where inspectors randomly select a specific number of units from a shipment to assess defects. The number of defects found within this sample determines whether the entire batch is accepted or rejected. Inspectors use AQL tables—such as those in the ANSI ASQ Z1.4 standard—to establish:
- Sample size: The number of units to be inspected based on the total shipment quantity.
- Acceptance level: The maximum number of defective units allowed before the shipment fails inspection.
Defects are categorized once the sample is evaluated into the three main types mentioned above. If the number of defective units surpasses the AQL threshold, the shipment fails inspection and must either be corrected, reworked, or rejected based on contractual agreements.
After inspection, a shipment certificate is issued to confirm whether the batch of products passes or fails—giving buyers transparency and confidence before the goods are shipped.
It's important to understand that AQL sets the threshold of acceptable defects—it does not promise a defect-free shipment. Beyond AQL, there’s also Rejectable Quality Limit (RQL)—the worst quality level that is outright unacceptable. If defect levels approach or exceed RQL, it signals severe quality issues, often leading to full shipment rejection without negotiation. Between AQL and RQL lies Indifference Quality Level (IQL)—a gray zone where decisions may depend on the buyer-supplier agreement.
Breaking Down General and Special Sampling Levels in AQL
When conducting AQL inspections, selecting the right sampling level is crucial for balancing inspection thoroughness with cost and time. The AQL guideline consists of two main types of sampling levels: General Sampling Level and Special Sampling Level, each designed for specific inspection needs.
General Sampling Levels
The General Sampling Level is the most commonly used method in AQL inspections and is typically applied to routine quality checks of mass-produced consumer goods. Within this category, three sub-levels determine how many units to sample based on the shipment (lot) size:
The ratio of sample size to lot size increases from GI to GIII. For mass consumer products, such as apparel, electronics, and home goods, GI and GII are typically used, ensuring a balance between inspection cost and confidence in product quality.
Special Sampling Levels
Special Sampling Levels are adopted for specific, non-standard purposes, such as when:
- Destructive testing is required.
- Critical safety components are being checked.
- Inspecting very small production runs or high-cost items.
Since these scenarios may require fewer units due to the nature of testing (like when the test destroys the product), Special Sampling Levels help adjust the inspection plan to fit the context without compromising on quality insights.
Random Sampling for Product Inspections
While zero defects are the ultimate goal, achieving this is often unrealistic, especially for non-safety-critical products. Random sampling helps balance quality assurance with efficiency, but it also comes with inherent risks—such as potentially rejecting a good-quality batch or accepting a defective one.
The flexibility of AQL allows businesses to adjust acceptance sampling levels based on factors such as:
- Budget constraints – Higher sampling levels can be more expensive but increase confidence in the results.
- Risk level of the product – Stricter AQL levels apply to higher-risk products (e.g., medical devices, automotive parts).
- Supplier trustworthiness – Well-established suppliers with a history of high-quality production may require less stringent inspections.
- Destructive testing requirements – If inspections involve destructive testing, sample sizes may need to be minimized.
Choosing the right sample size and AQL levels ensures a balance between cost and quality confidence, helping businesses make informed decisions.
Why Is AQL Important?
Given time and cost constraints, inspecting each product individually is often unrealistic, especially when dealing with large production runs. At the same time, checking just a single item is unlikely to give a reliable picture of overall quality.
This is where AQL provides balance — it defines how many units should be inspected and how many defects can be tolerated before a shipment is rejected. By applying AQL, businesses can:
- Gain a reliable snapshot of product quality without the burden of 100% inspection and reduce the risk of shipping defective products.
- Save time and costs, as only a representative sample of the total shipment is checked, making it a more efficient process, especially for high-volume orders.
- Establish clear acceptance and rejection criteria, ensuring that inspection results are objective, consistent, and actionable.
- Adapt inspection rigor based on product risk, using different AQL thresholds for various defect severities — for example, a tighter standard for functional checks and a more lenient one for minor cosmetic flaws.
- Strengthen supplier accountability by enforcing quality benchmarks.
How to Use the AQL Table
The AQL chart is a practical and standardized tool that guides quality inspectors in determining how many units from a shipment should be sampled and how many defects are allowable before the entire batch must be accepted or rejected. This approach brings objectivity to quality control and ensures alignment between buyers and suppliers.
To effectively use the AQL table, follow these steps:
- Determine the Lot Size: First, identify the total number of units in your shipment. This is your lot or consignment size.
- Choose the AQL Standard: Based on your product type and risk tolerance, select the appropriate AQL percentage. For example, you may use AQL 2.5 for major defects, 4.0 for minor defects, and 0.0 for critical defects that are unacceptable under any circumstances.
- Find Sample Size and Acceptance/Rejection Numbers: Cross-reference your lot size and inspection level in the AQL table to find the correct sample size and the corresponding acceptance and rejection numbers.
For example, if a brand orders 10,000 units of a product and selects a sample size of 315 units for inspection, the AQL 2.5 table might indicate:
- Acceptance number: 14 defects (shipment passes if defects are ≤14)
- Rejection number: 15 defects (shipment fails if defects are ≥15)
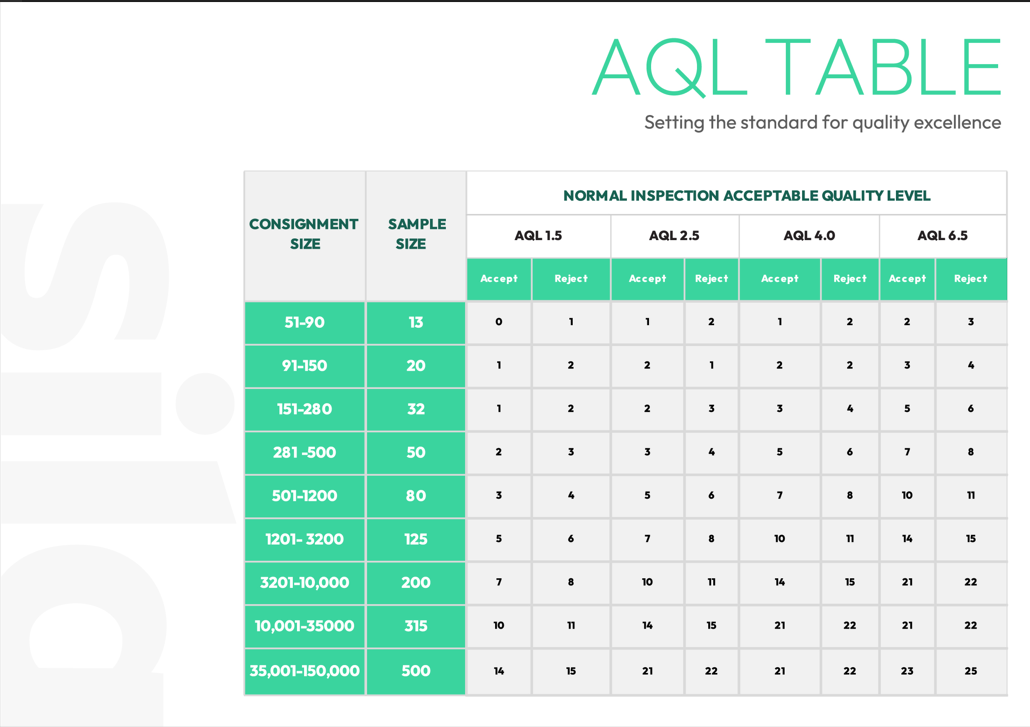
Why It Matters
Using the AQL table allows companies to:
- Set clear and consistent thresholds for accepting or rejecting shipments, reducing subjective decisions.
- Save time and cost by inspecting a representative sample rather than every single unit.
- Adapt inspection rigor depending on product type, volume, and risk.
- Communicate expectations clearly between buyers and suppliers, aligning on acceptable quality levels before production begins.
The Silq Advantage: Reliable AQL Inspections
At Silq, we go beyond traditional factory inspections — combining quality control with supply chain efficiency. By leveraging real-time data from factory floors, we not only ensure that brands receive high-quality products but also help optimize shipping timelines. This integration of inspections and logistics enables better planning and on-time delivery, reducing delays and costly surprises.
Our services include:
- Pre-shipment inspections – Conducted before products leave the factory, minimizing the risk of defective goods entering your supply chain.
- On-site factory audits – In-depth assessments of production processes and supplier quality controls to ensure ongoing compliance and reliability.
- Live inspections – Real-time inspections with instant updates and defect documentation, giving brands full visibility into what’s happening on the factory floor.
Why choose Silq for AQL inspections?
- Clarity on defect severity: We help ensure that your team and suppliers are aligned on what constitutes a critical, major, or minor defect, avoiding confusion and setting clear expectations.
- Visual defect reporting: Our inspectors provide detailed inspection reports with images and notes.
- Customized sampling plans: We tailor inspection sampling levels based on product risk, supplier history, and shipment size — saving you time and focusing on what matters most.
- End-to-end support: From quality control inspection booking to final reporting, Silq handles the process seamlessly, so you can focus on growing your business while we manage your product quality.
- Integrated inspection and shipping intelligence: By combining inspection insights with logistics planning, we help brands mitigate risks earlier and ensure smoother, on-time deliveries.
With Silq, you get more than just inspections — you gain complete visibility into your supply chain and a partner dedicated to protecting your brand, enhancing supplier accountability, and ensuring that only quality products reach your customers.
Read More: How Combining Inspections and Freight Forwarding Improves Efficiency
AQL as a Critical Quality Control Tool
AQL inspections are an industry-standard method for maintaining product quality while balancing time and cost. By setting clear AQL levels, importers can:
- Align quality expectations with suppliers.
- Detect and address defects before products reach customers.
- Minimize risks associated with defective goods.
At Silq, we make AQL inspections seamless and transparent—helping brands protect their reputation and ensure product excellence. Ready to take control of your supply chain? Get in touch with us today!
Frequently asked questions
Scheduling an AQL inspection with Silq is simple. Contact our team, specify your AQL requirements, and we’ll handle the rest—ensuring your products meet the highest standards before they are shipped.
If defects exceed the acceptable limit during inspection, the shipment fails. Typically, the supplier is responsible for corrective actions, which may include:
- Reworking defective units.
- Producing a replacement batch that meets AQL standards.
- Sorting the batch to separate acceptable from defective units.
- In extreme cases, if correction is not feasible, scrapping or recycling the batch.
The exact course of action will depend on the terms agreed upon in the contract, but suppliers usually bear the cost of remediation.