As international trade continues to play a significant role in global economics, more businesses, especially those in the SMB category, are leveraging it to reach more customers and access various suppliers worldwide.
However, international trade can be complicated for these SMEs because of the nuances and complexities involved, which is why third-party factory inspections have become necessary.
Factory inspections have become an invaluable shipping service these businesses can leverage to enhance efficiency and scheduling in their manufacturing and shipping operations. However, they can be complicated and, in many cases, lead to costly mistakes that can destroy the supply chain. This article will review these mistakes and explore the factory inspections best practices for avoiding them.
What are Factory Inspections & Why Are They Important?
Factory inspections are systematic reviews of the manufacturing process offered by third-party agents or freight forwarders like Silq.
Through these inspections, your business can maintain quality, ensure regulatory compliance, and build trust with their customers worldwide. You can also leverage this to identify issues in production that could lead to costly delays or recalls.
Silq offers various types of factory inspections, some of which include:
1. Factory Audits: This is a detailed on-site audit to evaluate infrastructure, capacity and capabilities assessment, environmental impact certificate verifications, labor practices, etc.
2. PP (Pre-Production) Sample Inspection: This ensures your final product meets design specifications, quality standards, and customer expectations before mass production.
3. Inline Inspection: Early detection helps you ensure that only top-quality products leave the production line. It is necessary because corrective actions should be taken in the early stages.
4. Final inspection: This ensures all products are defect-free and meet Global AQL Standards.
Tips to Prepare for a Factory Inspection
Preparing for a factory inspection ensures a smooth and successful process. Here are some steps to help you prepare:
- Understand the Inspection Requirements: Familiarize yourself with the relevant regulations, industry standards, and buyer specifications that apply to your factory. This knowledge is essential for ensuring compliance and meeting customer expectations.
- Define the Scope & Objectives: Clearly outline the areas and processes that will be inspected, and identify the objectives you want to achieve through the inspection. This helps set clear expectations and ensure that all critical aspects are covered.
- Choose a Third-Party Inspection Company: Select a reputable and experienced inspection agency like Silq that has expertise in your industry. A well-chosen partner can provide valuable insights and help you navigate the complexities of the inspection process.
- Communicate with the Factory: Ensure that the factory authority is aware of the inspection requirements and expectations. Provide any necessary documentation or information to facilitate a smooth inspection process.
- Review Documentation and Records: Gather and review all relevant documentation and records related to the factory’s operations, including production procedures, quality control records, and supplier agreements. This preparation helps identify potential issues and ensure all necessary information is readily available during the inspection.
Common Mistakes Businesses Make During Factory Inspections
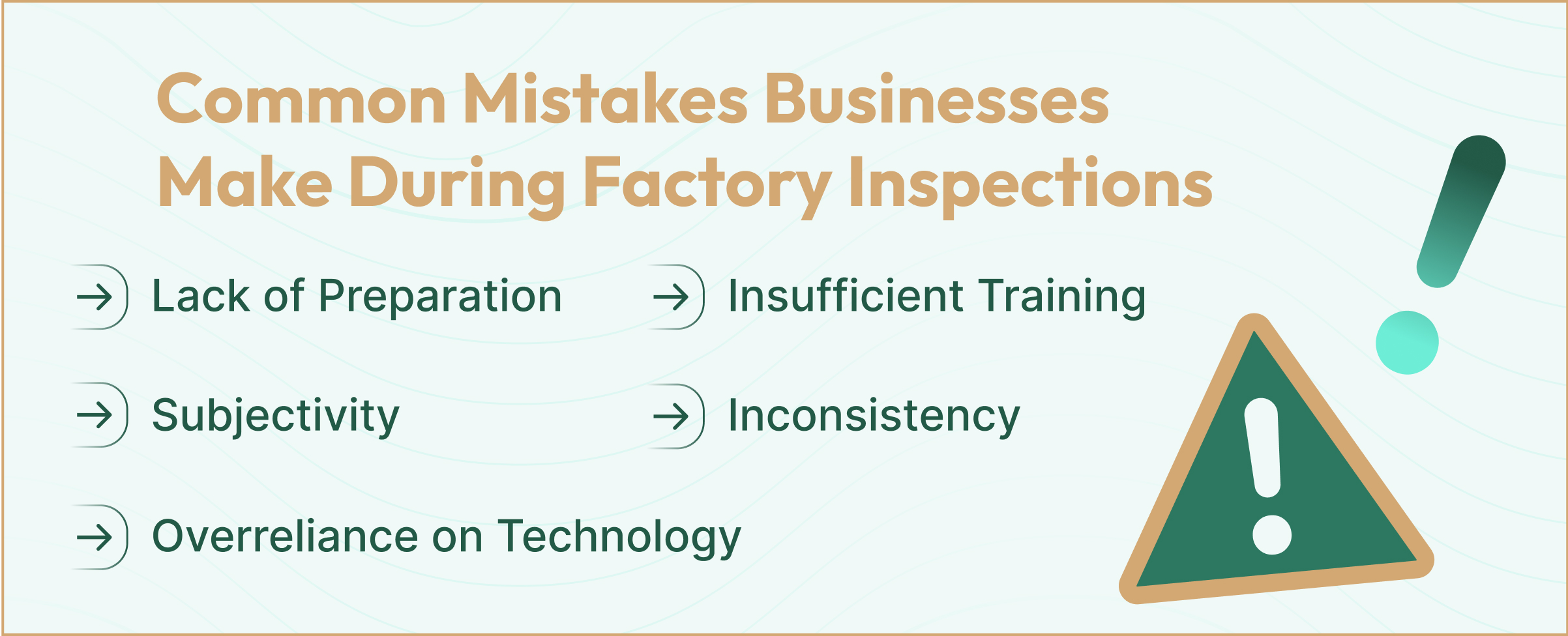
Although third-party factory inspections are powerful solutions for SME businesses, many times, they can have the opposite effect, such as making things worse for the supply chain, leading to disruptions and crippling financial implications.
Here are some factory inspections mistakes to avoid, as a shipper.
1. Lack of Preparation
Failing to prepare adequately can result in significant setbacks, making achieving the desired outcomes from the inspection difficult. Without a clear plan for the inspection process, businesses may miss setting proper expectations, particularly regarding manufacturing and shipping standards.
Similarly, if inspectors are not well-prepared — due to limited understanding of the business, lack of expertise, or insufficient resources — they may fail to identify critical issues that could impact quality. This can lead to overlooked defects, production delays, and wasted resources, ultimately disrupting the supply chain. Proper preparation ensures a thorough inspection and reduces the risk of costly oversights.
2. Insufficient Training
When the inspectors are untrained, it can be challenging because they won't easily identify critical issues that can impact the overall manufacturing and shipping processes. There is also the situation where the inspectors are properly trained in one area, such as production, but cannot evaluate other areas, such as shipping. Lack of training can compromise the reliability of the inspection process.
3. Subjectivity
There are many cases whereby business or third-party inspectors rely on personal judgment rather than objective criteria. This usually happens when there is inadequate information or wrong assumptions. Subjectivity can introduce variability into inspections. Ensuring inspections are based on clear, measurable standards helps remove subjectivity and ensure fairness and accuracy.
4. Inconsistency
Inconsistent inspection methods and criteria can lead to confusion and unreliable results. Every inspector must follow the same procedures, using the same standards and tools to maintain uniformity across inspections. Without this, you risk releasing subpar products to the market.
5. Overreliance on Technology
Tech solutions like automation, AI, and ML can help streamline and enhance inspections but cannot entirely replace human judgment. Although they can help inspectors and your supply chain detect defects or irregularities, they have limitations. That is why a balance between tech solutions and human oversight is essential for effective inspections.
Best Practices For Successful Factory Inspections
With a platform like Silq, you can enjoy real-time visibility and detailed reports for inspection data, which helps curb many of these mistakes. However, in the wake of mounting disruptions, there are best practices that make factory inspections successful for SME businesses, especially for enhancing shipping and manufacturing operations.
Some of these include:
1. Clear Inspection Criteria
Before embarking on any inspection in the production and shipping processes, whether in-house or via a third party, it is essential to have a clear objective for success. This way, all stakeholders are on the same page before going in.
Having a clear inspection criterion ensures accurate and consistent evaluation of the product. However, both parties must ensure an outline of the inspected processes, how they will be evaluated, and the acceptable tolerances for variation.
2. Standard Operating Procedures (SOPs)
Standard operating procedures ensure the inspections can be carried out and measured consistently across different locations, teams, and situations. This way, all stakeholders can eliminate errors and confusion from the entire operation. They also provide a step-by-step guideline for conducting inspections.
3. Qualified Inspectors
Although inspections are necessary, they can be challenging when done wrong, and a key part of that is leveraging the wrong or inexperienced factory inspectors. That is why Silq continues to play a successful role for SME businesses across the globe.
We understand what our clients need and invest in the right expertise, tools, and resources to ensure we can identify issues more accurately and handle the inspection process with greater precision.
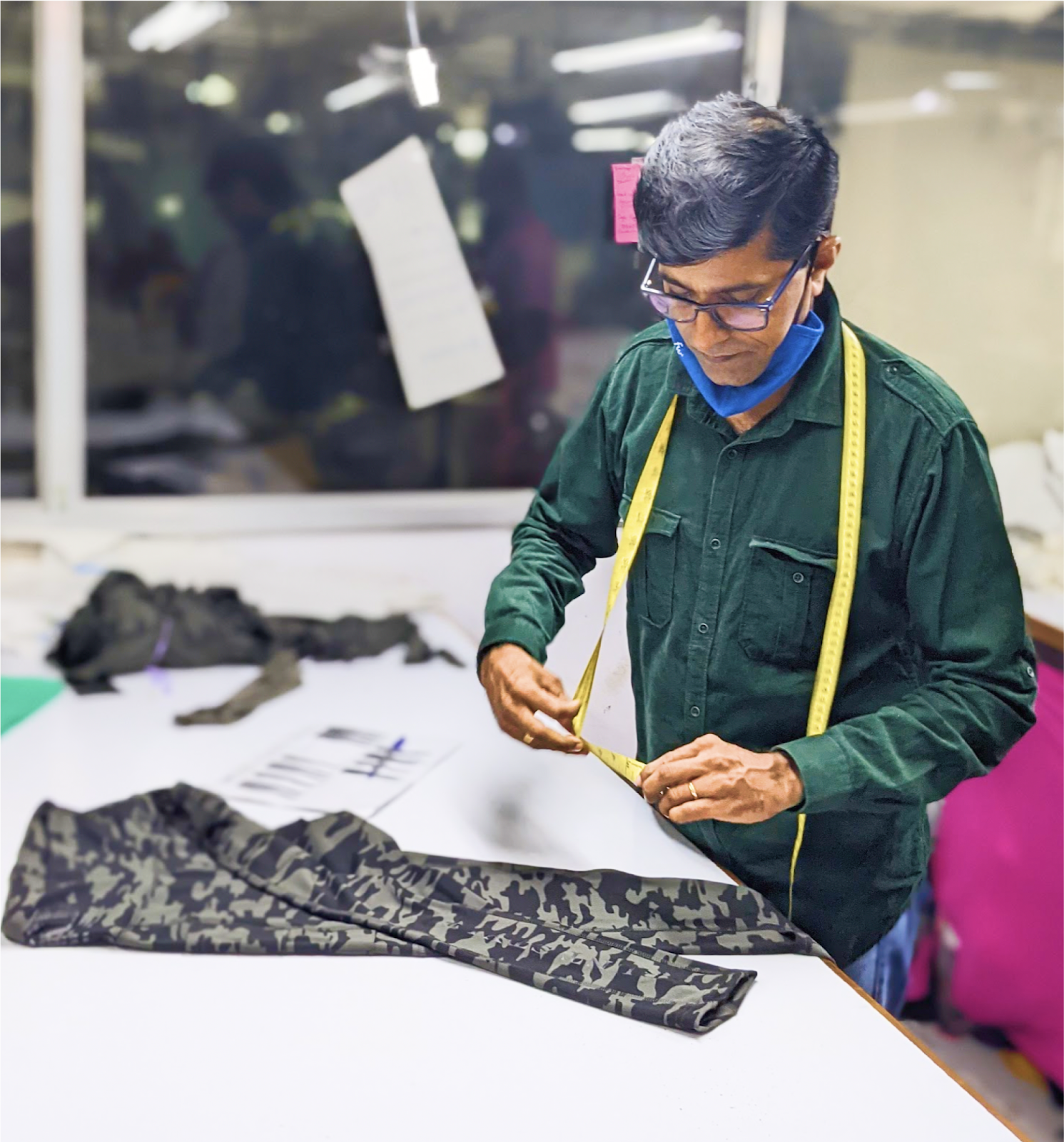
4. Accurate and Effective Documentation
Accurate and thorough documentation is essential for tracking the results from the final inspection, mainly because it allows small or medium businesses to identify patterns and ensure compliance with quality standards.
Proper record-keeping allows you to review past inspections, identify areas of improvement, and ensure transparency in their quality control processes.
How Silq Transformed Manufacturing & Shipping For a Merchandise Company
A small fashion merchandise company was excited to expand internationally. But as orders grew, so did the challenges. Customers complained about inconsistent quality, delayed deliveries, and defective items. The company operated a streamlined process to the best of its ability, but disruptions and issues kept popping up until the company sought help.
The company partnered with Silq, a third-party inspection service, to fix its production process.
The first thing Silq did was introduce structured inspections with clear criteria. This eliminated most of the confusion the company faced about what to check during each step of production. Silq also brought in experienced inspectors who identified problems the fashion business had missed and worked together to create standard operating procedures (SOPs) for inspections.
The real game-changer was combining technology with human oversight. While machines caught visible defects, Silq's inspectors used their expertise to catch subtler issues. Over time, the company noticed a dramatic improvement in quality and delivery times. Complaints decreased, and the company's customers began to trust the brand again. Thanks to Silq's inspections, the small business continued to thrive in the global market.
Factory Inspection & Freight Forwarding Prowess in One Platform
Silq is a digital freight forwarder that allows insightful and reliable factory inspections. This ultimately ensures that small businesses and medium-sized enterprises can enhance the quality of their products while shipping on time.
We combine the two to protect your brand, supply chain management, and bottom line.
With our services, you can have the shipping advantage of large companies. With fewer employees, you are sure of frequent shipping, diversification of shipping operations, and cost savings on unused space. Get started now.
Frequently asked questions
1. Skipping pre-inspection planning, leading to unclear expectations.
2. Relying on supplier reports, increasing bias risks.
3. Inspecting too late in production, making defects harder to fix.
Silq provides:
1. Unbiased, real-time quality reports for quick decisions.
2. Trained on-site inspectors to spot defects early.
1. Set clear quality standards before production.
2. Use a standardized inspection checklist for consistency.
3. Leverage third-party inspections like Silq for unbiased audits.
1. Suppliers may prioritize shipments over quality.
2. Hidden defects and compliance failures are harder to detect.
3. Lack of independent verification increases risks.
1. Tech-driven compliance checks for regulatory adherence.
2. Real-time reports for better visibility.
3. On-ground auditors for unbiased defect assessment.